February 21, 2025 - 7 minutes read
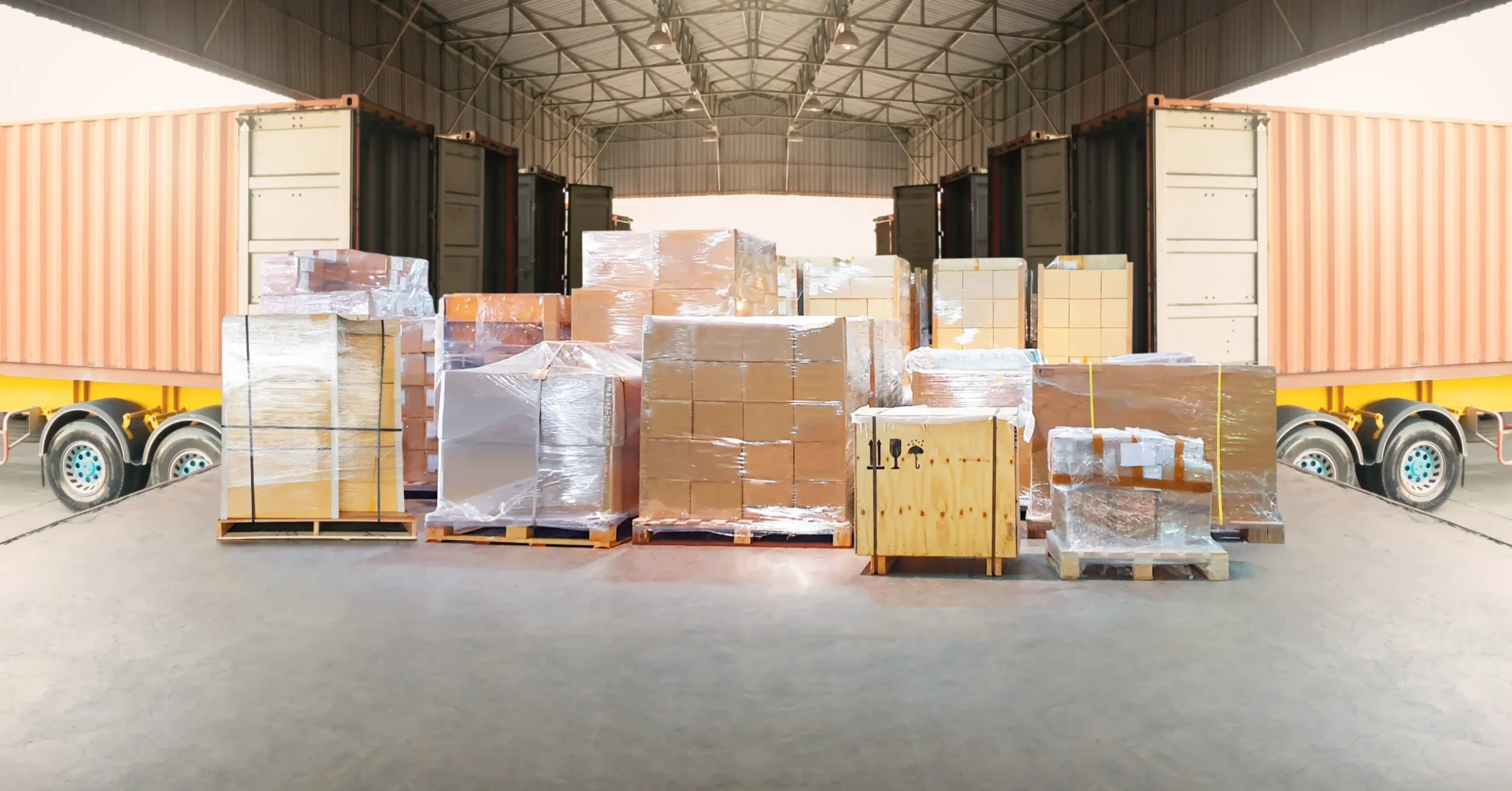
Improving OTIF Performance Through Supply Chain Visibility & Collaboration
In today’s increasingly competitive global market, retailers and suppliers are constantly under pressure to meet on-time and in-full (OTIF) delivery standards. Falling short can lead to costly chargebacks, lost revenue, and strained customer relationships. Despite this reality, many companies still operate with limited supply chain visibility, disconnected systems, and outdated processes—making it challenging to improve OTIF metrics.
Strong OTIF performance requires two fundamental components: real-time supply chain visibility and collaboration between teams. This article explores how better data and communication can drive improvement and what metrics companies need to track to stay ahead. It also presents Agistix’s solutions for closing visibility gaps, connecting supply chain partners, and optimizing fulfillment from end to end.
What is OTIF and why does it matter?
OTIF is a critical supply chain KPI that measures logistics performance. It refers to a supplier’s ability to deliver goods within the requested delivery windows and in full quantities ordered.
Originally introduced by Walmart in 2017, OTIF was designed to hold suppliers accountable for meeting delivery commitments. The initiative inspired the retail industry to adopt similar performance standards for operational efficiency and reliable fulfillment.
A strong OTIF score signals an efficient supply chain, while missed deliveries can result in penalties and substantial margin erosion. Here’s why OTIF performance matters:
- Stronger customer relationships – Reliable, on-time deliveries increase trust and satisfaction, driving repeat business.
- Lower operational costs – Meeting OTIF targets reduces the need for last-minute expedited shipments to resolve late shipments and shortage issues.
- Improved supply chain efficiency – A history of on-time, in-full deliveries strengthens collaboration with suppliers and carriers.
- Fewer disruptions – High OTIF rates prevent delays, inventory shortages, and unnecessary reworks.
The most significant barriers to OTIF performance occur at critical supply chain touchpoints. The majority of missed on-time requirements can be traced back to three key issues: dock scheduling, carrier pickup, and transportation delays. Addressing these root causes is essential for improving fulfillment reliability and minimizing disruptions.
The role of supply chain visibility in OTIF performance
True supply chain visibility requires a connected ecosystem where critical information flows easily between all stakeholders. This interconnectedness empowers businesses to improve OTIF supply chain scores by providing a clear, real-time view of their entire operation:
- Visibility tools act as an early warning system, helping detect unforeseen disruptions like port closures, weather conditions, or transportation delays. Live alerts allow shippers to address issues quickly by rerouting shipments or utilizing alternative modes to ensure on-time delivery.
- Supply chain visibility is more than simply tracking shipments. It should also include monitoring carrier performance, identifying opportunities to optimize routes or consolidate shipments, and tracking routing compliance to establish a more effective and reliable supply chain network.
- Visibility platforms offer insight into freight costs, helping compare expected charges to actual invoices, identify discrepancies, and uncover opportunities for savings. A granular view of financial data provides better budget control and smarter negotiations with carriers.
What’s more, visibility platforms are hubs for information sharing, providing suppliers, carriers, and internal teams with real-time data and performance metrics. If a supplier delays production or a carrier declines a load tender, visibility allows all parties to adjust their plans to keep things on schedule.
The power of collaboration in driving OTIF excellence
Effective collaboration is a key factor in achieving high OTIF performance. In fact, recent surveys show that 56% of manufacturers with excellent supply chain collaboration report supplier on-time delivery of more than 95%. When suppliers, carriers, and retailers work in sync—sharing data, aligning schedules, and proactively addressing disruptions—OTIF targets become far more attainable.
- Greater supply chain efficiency
Suppliers, carriers, and retailers working together readily identify and resolve issues faster to improve delivery accuracy. - Better communication and transparency
Real-time data sharing allows stakeholders to view shipment status, inventory levels, and demand forecasts. Such shared understanding minimizes misunderstandings and aligns efforts toward achieving high OTIF rates. - Increased predictability and reliability
Strong collaboration establishes more accurate delivery windows, as evidenced by Kraft Heinz, which improved its OTIF score by 12% through a focused approach to carrier relationships and enforced collaborative planning. - Cost efficiency
Collaboration improves demand forecasting, reduces excess inventory, and minimizes the need for costly expedited shipping. By working together, supply chain partners can also share logistics resources—such as transportation assets—to cut costs while improving delivery performance. - Shared responsibility
Close collaboration among suppliers, carriers, and internal teams creates shared responsibility for performance, encouraging proactive communication and joint problem-solving.
Practical steps to improve OTIF through visibility and collaboration
Improving OTIF performance requires the right combination of tech, process improvement, and strong supply chain partnerships. Here are actionable steps to consistently improve delivery performance and fulfillment reliability.
Step 1: Invest in visibility technology
A strong OTIF strategy starts with real-time visibility. Investing in an end-to-end visibility platform enables accurate tracking, data-driven decision-making, and collaboration across the supply chain. The right solution should provide:
- Complete shipment visibility – Track every shipment, across all modes and carriers, from origin to final destination.
- Integrated rating and booking – Centralize multimodal shipment management and carrier selection within a single platform.
- Collaboration tools – Enable self-service access to critical data and simplify communication between stakeholders.
Step 2: Improve order fulfillment
Automating key processes, improving warehouse layouts, and refining picking and packing workflows reduce errors and speed up fulfillment. Warehouse automation technologies streamline operations, while predictive analytics improve inventory accuracy and prevent stockouts.
Step 3: Utilize transportation management solutions
A well-integrated transportation management system (TMS) helps optimize shipping routes, minimize delays, and improve cost-effective carrier selection. Performance data ensures reliable carrier choices, while exception management tools help resolve disruptions before they impact OTIF.
Step 4: Foster collaborative behavior
Clear communication and data sharing improve coordination between suppliers, carriers, and retailers. Aligned KPIs create accountability, digital collaboration tools enable real-time problem-solving, and strong partnerships drive consistent delivery performance.
Key metrics to track for OTIF success
A widely accepted OTIF benchmark is 95%, meaning 95 out of every 100 orders are shipped complete and on time. In competitive markets, some companies push for even higher standards, aiming for 99% or more. Achieving and maintaining this level of OTIF performance requires tracking the right metrics to identify inefficiencies and make data-driven improvements.
Here are the key KPIs that supply chain professionals rely on:
- On-time delivery rate – Measures the percentage of orders that arrive on or before the promised delivery date.
- Order fill rate – Tracks the ability to fulfill orders completely from available inventory.
- Inventory turnover – Indicates how quickly inventory moves through the supply chain.
- Average delivery time – Calculates the average time it takes for an order to reach the customer.
- Customer order cycle time – Measures the total time from order placement to final delivery.
This formula is widely accepted for OTIF calculations:
Improving OTIF performance with Agistix
Improving OTIF demands real-time visibility, proactive decision-making, and collaboration every step of the way. Agistix gives businesses the tools to take control, providing automated data capture and in-depth analytics to eliminate blind spots and address disruptions before they impact delivery performance.
Agistix’s platform includes three solutions that can be used independently or as a comprehensive logistics suite:
- Agistix Visibility – Monitors shipments across all modes and carriers, tracks key performance indicators, and provides a complete view of supply chain operations.
- Agistix TMS – Optimizes route planning, carrier selection, and transportation management to improve delivery efficiency.
- Agistix Microsites – Enables stakeholders to access real-time shipment data through a self-service platform.
OTIF performance is a direct reflection of supply chain efficiency. Agistix delivers the visibility, control, and intelligence businesses need to meet delivery commitments with confidence. Book a demo today to see Agistix in action.